XW Type Curved Track Conveyor Line
Classification:
Key words:
FAQ
Details
Products
Inquiry
Case
FAQ
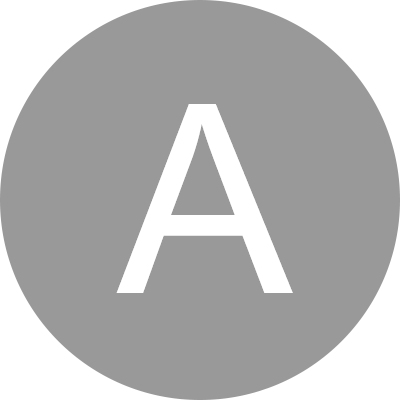
Under normal circumstances, it is not allowed. Above 60Hz (there are also modes above 50Hz), with constant voltage, it generally has a constant power characteristic. When the same torque is required at high speeds, attention must be paid to the selection of the motor and inverter capacity.
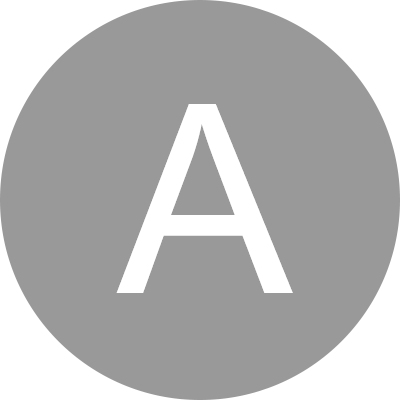
Power can still be output below 6Hz, but depending on conditions such as motor temperature rise and starting torque, the minimum operating frequency is set around 6Hz. At this point, the motor can output rated torque without causing serious heating issues. The actual output frequency (starting frequency) of the inverter varies by model, ranging from 0.5 to 3Hz.
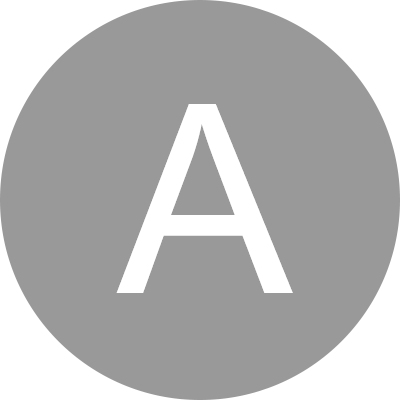
When the frequency decreases, the voltage is reduced in direct proportion. Since the AC impedance decreases while the DC resistance remains unchanged, this will tend to reduce the starting torque at low speeds. Therefore, at low frequencies, to achieve a certain starting torque, the output voltage should be increased somewhat when V/f is given. This compensation is called enhanced starting. Various methods can be used to achieve this, including automatic methods, selecting V/f modes, or adjusting potentiometers.
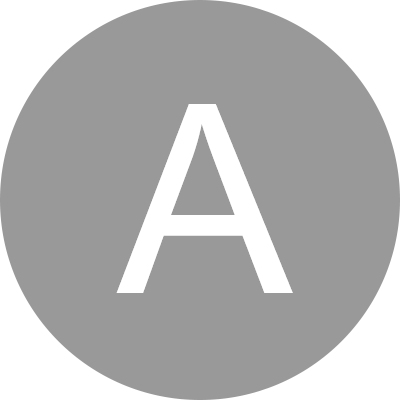
When the frequency decreases, the voltage V also decreases proportionally. This issue has been explained in answer 4. The proportional relationship between V and f is predetermined considering the motor characteristics, and several characteristics are usually stored in the controller's storage device (ROM), which can be selected using a switch or a dial.
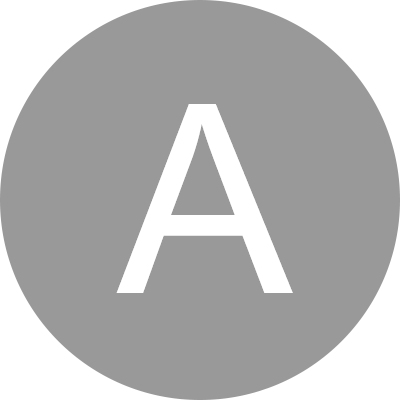
Using a frequency converter for operation, the frequency and voltage increase correspondingly with the acceleration of the motor, and the starting current is limited to below 150% of the rated current (depending on the model, it can be 125% to 200%). When starting directly with a power frequency supply, the starting current is 6 to 7 times higher, which can cause mechanical and electrical shocks. Using a frequency converter allows for a smooth start (the starting time is extended). The starting current is 1.2 to 1.5 times the rated current, and the starting torque is 70% to 120% of the rated torque; for frequency converters with automatic torque boost function, the starting torque can exceed 100%, allowing for full load starting.
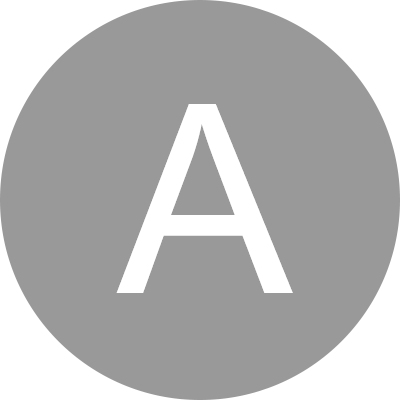
When the frequency decreases (low speed), if the output power remains the same, the current increases, but under the condition of constant torque, the current remains almost unchanged.
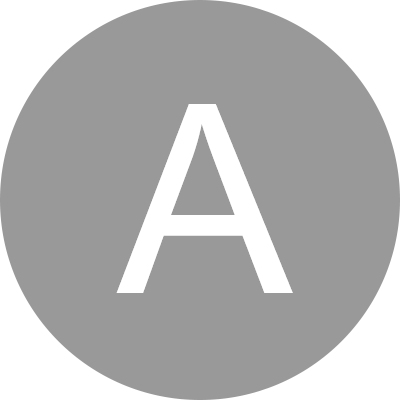
The torque of the motor is generated by the interaction between the magnetic flux and the current flowing through the rotor. At the rated frequency, if the voltage is constant and only the frequency is reduced, the magnetic flux becomes too large, the magnetic circuit saturates, and in severe cases, it can burn out the motor. Therefore, the frequency and voltage must change proportionally, meaning that while changing the frequency, the output voltage of the inverter should be controlled to keep the magnetic flux of the motor constant, avoiding weak magnetism and magnetic saturation phenomena. This control method is often used in energy-saving variable frequency drives for fans and pumps.
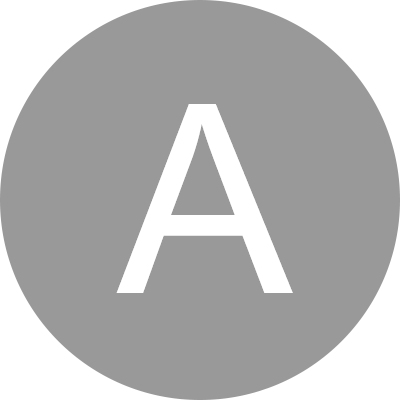
The main circuit of the inverter can be roughly divided into two categories: the voltage type, which converts the DC of a voltage source into AC, with the filtering of the DC circuit done by capacitors; and the current type, which converts the DC of a current source into AC, with the filtering of the DC circuit done by inductors.
Product Introduction
Product Introduction:
The XW box-type curved track conveyor line is a patented product of our company, widely adopted by companies such as Jilin Lightweight and SANY Heavy Industry (Shenyang). We welcome inquiries.
The XW curved track conveyor line is uniquely designed by our company, matching the box-type curved track with the Kaito chain electric hoist, making it particularly suitable for automated production lines. Compared to traditional I-beams, the box-type curved track has advantages such as high wear resistance and good stability, receiving widespread praise from users.
Analysis of the causes leading to severe wear of the curved section of the monorail track
Production assembly lines and logistics companies often use electric hoist monorail trolleys as medium and small lifting equipment to facilitate material movement. The tracks for monorail trolleys typically use ordinary hot-rolled I-beams. This type of profile has poor wear resistance, and with frequent use, the track wears significantly, especially in the curved sections. The main reasons include the low strength and hardness of the Q235 material itself, and the plastic deformation that occurs during the forming process of the curved section (the outer edge becomes thinner or even tears under tension, while the inner edge is compressed and may wrinkle).
Plastic deformation occurring in the forming process of the curved section leads to:
- Increased longitudinal pressure on the free edge of the lower flange, which becomes thinner and eventually curls up and is scrapped over time;
- Wrinkles on the inner edge arc due to compression, causing the hoist trolley to run unevenly and resulting in shaking (impact);
- Uneven thickness on both sides of the lower flange causes the hoist trolley to tilt, leading to uneven wheel pressure distribution.
The above issues are important reasons for the wear of the curved section of the track.
Solutions to improve severe wear of the curved section of the monorail track
- Change the ordinary hot-rolled I-beam Q235 to a high-strength and high-wear-resistant Q345 welded box track.
- Replace hot bending or cold bending with CNC contour cutting to avoid the above defects caused by plastic deformation during processing.
- Change the track from ordinary I-beam to welded box track, transforming the flange from an inclined surface to a flat surface, and using drum wheels instead of conical wheels to adapt to the operation of the curved section, ensuring that the wheels maintain pure rolling during operation on the curved section.
Use two sets of anti-wheel edges instead of conical wheel edges to reduce friction.
Technical Implementation:
Box track and its components
- In terms of materials, I-beams use Q235, which has poor wear resistance, while box tracks use Q345 (16Mn), which is a low-alloy high-strength structural steel with high wear resistance.
- From a structural perspective, the flange plates of I-beams are thin and easily worn. When wear reaches a certain level, the mechanical properties of the metal material significantly decline, necessitating track replacement every 1-2 years. In contrast, the flange plates of box tracks can thicken with increased load, and their strong wear resistance results in minimal wear, greatly extending their service life.
- From a mechanical perspective, compared to I-beams, the inertia of the X and Y axes of box tracks is greatly increased, reducing deformation and enhancing stability. Based on these characteristics, it is possible to reduce the number of support points or lifting points in straight sections, leaving space for on-site layout.
Box track and its components
Connection:
- Use clamps for positioning to ensure coaxiality, and connect with bolts.
Single electric hoist type
Single electric hoist type (double)
Double electric hoist type
On-site use
The XW box track conveyor line developed and produced by our company has been gradually put into use in enterprises such as Jilin Lightweight. During use, the hoist trolley runs smoothly on the box track, and the wear of the curved track has significantly improved, greatly increasing its service life.
Previous Page:
Next page:
Online Inquiry
Fill in your phone number and E-mail information, and we will contact you as soon as possible.
Case
Leave your needs here.
Please leave your needs and we will contact you as soon as possible!

Service Hotline
Manufacturing address:intersection of Caibin West Street and Deren Road in Changchun China-Korea (Changchun) International Cooperation Demonstration Zone
Service Address:No.3 Fumin Street, Lvyuan District, Changchun City
Website:www.兴泰起重.中国
www.crane-china.cc
WeChat service number: xingtaiqizhong
Zip Code:130012
Sales Advisory Phone:400-044-6608/13578886608WeChat Synchronization (Mr. Zhang)
After-sales service telephone:18343082566(Mr. Yu)/400-044-6608
Landline:0431-87096377
Fax:0431-87096377
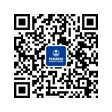
Copyright:Changchun Xingtai Crane Machinery Co.,Ltd